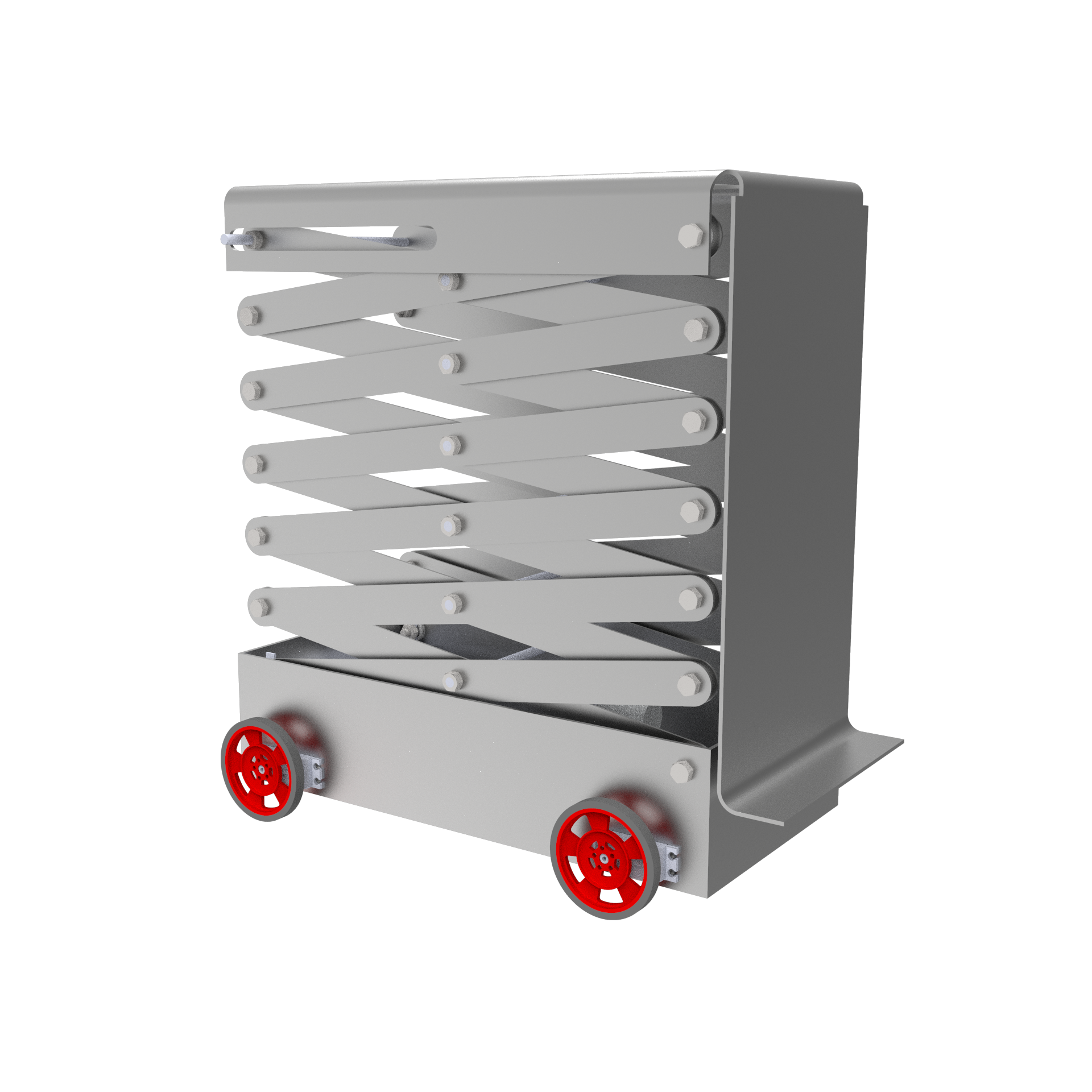
Lead Screw Scissor Lift
Course & Project Background
Design and Manufacturing or 2.007 as it is more frequently called is a course aimed to sharpen both your machine shop skills as well as understanding how to best design something given certain conditions and restraints. Every year students are asked to manufacture a robot that will compete in a competition at the end of the semester. The rules and restraints for this competition change every year forcing students to different strategies and designs.
Competition Rules
The competition board for 2020 was titled "Legacy" and was an homage to Professor Woodie Flowers who created the class. It also sampled some of the challenges from competition boards in the past. The game board can been seen on the right and the main components involve flower spinning, beaver lift, and collecting balls into a bin. Each allotting different amounts of points based on success and speed. The competition is only 120 seconds with the first 30 seconds being strictly autonomous and then next 90 being RC controlled. The starting position may be anywhere in the colored section but must be within the size constraints of 16" cube.
Strategy Development
First, I fully understood the rules to identify effective strategies. I outlined five point strategies, exploring their potential success. The top two were Beaver Lift and Multiplier, along with a Beaver Lift and Flower Spin combo. Both yielded over 150 points, but I chose the Beaver Lift with Flower Spin for the Pachinko Balls. My goal was to lift the beaver to its max height and spin the flower to release the balls on the Pachinko Board.
Concept Generation
Next began the process of thinking of different methods of completing my Lift/Spin strategy. This involved thinking about what types of systems I could use to complete these tasks. All ideas were on the table at first including: scissor lift, pulley lift, and even the idea of developing a fan to produce lift. Most of the ideas had very little practicality leading me to choose the concept involving two robots which would each preform either the lift or the spin. The lift would be using a lead screw scissor lift and the spin robot would be incredibly minimal focused on slowly spinning the flower.
3D Modeling
It was at this point that COVID-19 had caused all of us to leave campus meaning that completing the physical robot and machining the parts was no longer possible. I proceeded to 3D model my entire robot on Solidworks creating 28 separate parts and then compiling them into a final assembly consisting of over 180 pieces.